In the 1980s, diesel engines were not seen as the stump-pulling powerhouses they are today, but as the magic bullet solution to high fuel prices and the abysmal fuel economy of gas-guzzling American V8s. And so, General Motors tried to create the Holy Grail of diesel V8s: an engine that produced respectable power while still sipping fuel at a miserly rate compared to similarly sized gasoline-burning engines. The result was the General Motors Detroit Diesel, a 6.2-liter diesel V8 that succeeded in its mission of saving money, but also suffered a slew of problems that would eventually earn it and its 6.5-liter companion a spot on the list of most-hated diesels. But was it really that bad? Let’s take a look.
The diesel engines of today are known for their stellar fuel economy and impressive power numbers, but that wasn’t always the case. For four decades, trucks all over America and the world have driven on the might of dependable Cummins, Duramax, and Power Stroke engines. The most famous of which are the Cummins 5.9-liter straight-six, International/Ford 7.3-liter Power Stroke V8, and the General Motors 6.6-liter Duramax LBZ. Then there are the infamous passenger car diesels of Volkswagens and others out there.


Just a few years before the 1984 launch of the Cummins B Series, diesel engines weren’t a symbol of power, but one of fuel economy and depending on the engine, reliability. You didn’t buy a diesel because you felt like you wanted to pull a train through the Wasatch Range, but because you couldn’t afford to keep on fueling your truck’s 10 mpg V8 gasser.
Prior to the multiple oil crises of the 1970s, truck diesels usually lived in medium- and heavy-duty equipment. I’m talking about straight trucks and semi-tractors. These engines were practically the size of Smart Fortwos all on their own and sang the kinds of songs we don’t hear on the open road anymore. However, there were experiments in putting diesel power into regular pickup trucks.
It’s debated which company was the first to put a diesel engine into a pickup truck, but it’s commonly reported that Dodge first experimented with a diesel pickup in 1962 with the Dodge W300. International Harvester had its own diesel pickups at about the same time with its C-1100 to C-1300 trucks. Both companies saw that there was a strong interest in diesel engines in medium-duty trucks and figured people would also want diesel power in pickup trucks. As it turns out, Dodge and International Harvester were right, but were also perhaps a decade too early.
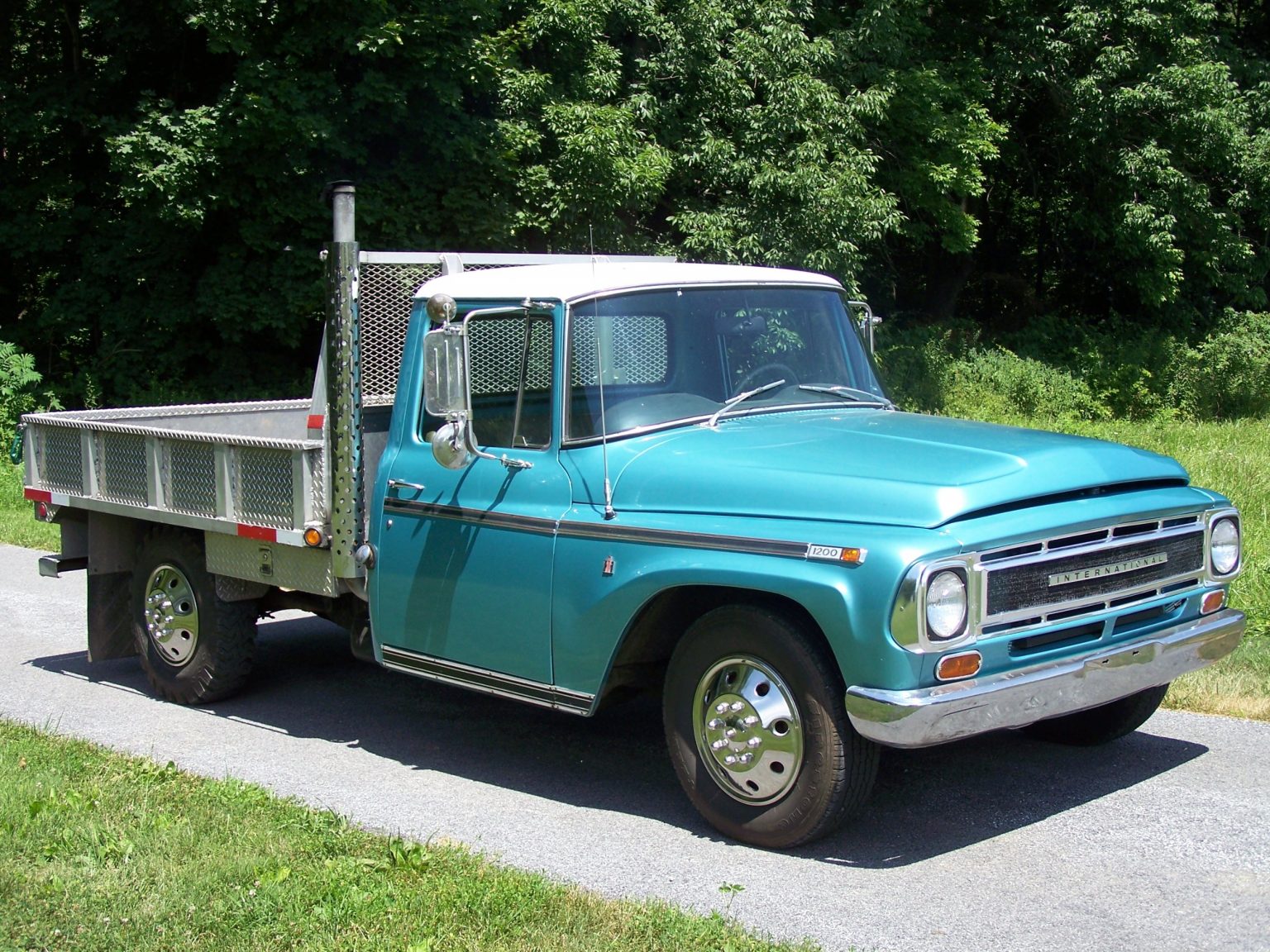
General Motors had long been in a special place when it comes to diesel engines. For decades, General Motors was essentially an unstoppable force. The General spread its wings far and wide. If you took a commuter train, it was nearly guaranteed that the power at the front of the train was built by GM’s Electro-Motive Division. If you shipped your goods by a truck, chances are that truck was powered by a Detroit Diesel engine. General Motors dominated diesel so much that its engines often became the default option for buses, emergency equipment, military vehicles, and even some watercraft.
Sadly, General Motors doesn’t have nearly the grasp it used to on diesel, but if you were alive several decades ago, there was a chance that your life depended on a GM diesel at least for something.
This domination of diesel would come in handy during the 1970s. America suffered from multiple fuel crises and a weakened economy while auto manufacturers faced more stringent fuel economy and emissions standards. Large gas-guzzling land yachts fell out of vogue while affordable, economical imports became sizzling hot. At the time, America’s gasoline engines found themselves choked out by emissions equipment, and they still didn’t get that great fuel economy. The answer for some automakers was to chase the holy grail of fuel economy: The diesel engine.
GM made a bizarre decision back then. It owned Detroit Diesel and could have used the company for help. Instead, GM’s passenger vehicle diesel would come from Oldsmobile. But, GM ran the program on a shoestring budget and demanded the engine go into production quickly. Oldsmobile engineers delivered, but what GM got was an engine rushed into production and based on a gas engine’s architecture, with disastrous results. An engineer who allegedly warned GM about its mistake was sacked. Well, 10,000 people across 14 states demanded a uniform redress program from GM, so GM probably should have listened.
It looked like General Motors did just that when it came time to put another diesel on the market.
What GM Should Have Done In The First Place
When it came time to launch a new diesel engine, General Motors went to the place it should have gone to in the first place, its Detroit Diesel subsidiary. The engine manufacturer did not have experience in building light-duty truck engines, but it had an established record of building practically bulletproof truck, bus, and locomotive powerplants.
Detroit Diesel says it built its first four-cycle diesel engine somewhere in the timeframe between 1970 and 1986. This engine predates one of the best-selling diesel engines of all time, the legendary Detroit Diesel Series 60 straight-six four-stroke, which was released in 1987.
History is fuzzy on what exactly was the first four-cycle Detroit Diesel, and even the company itself doesn’t say. Some sources point to the unloved and gutless 1980 8.2-liter “Fuel Pincher” diesel V8, which went into heavier applications such as box trucks and school buses, as Detroit’s first four-stroke. What I can say is Detroit Diesel made its fortunes and fame on two-cycle screamers, but the 1980s demanded the higher fuel economy offered by a four-cycle, so Detroit Diesel began cranking out the engines.
While I have not been able to find a full development history on the Detroit 6.2, I have been able to figure out its objective. As I said earlier, the early 1980s were a time when diesels were more for fuel economy than power. In Detroit Diesel’s own advertising, the GM subsidiary mentions that the 6.2-liter diesel merely has “enough power” for heavy pulling, then the marketing copy spends the rest of the time explaining how this engine is really going to save you a ton of money.
Unlike the Oldsmobile Diesel, the Detroit 6.2-liter V8 diesel was designed to be an oil burner from the start. Detroit says the secret sauce of the 6.2 V8 was its compression ratio, which was a sky-high 20.3:1. The engines were of a 2-valve pushrod valvetrain design and while they weren’t based on gas architecture, 6.2s were meant to be dropped directly to the existing engine bay infrastructure of GM trucks of the day. When combined with a Stanadyne DB-2 rotary injection pump, the same used by other diesels at the time, Detroit said its naturally aspirated cast iron block engines burned diesel fuel “very completely.”
No matter if the engine is idling or pulling, Detroit claimed that the 6.2-liter would get better fuel economy than comparable gasoline engines. These engines had water separators and block heaters, too, showing some lessons learned from the Oldsmobile diesel debacle.
In April 1982, Four Wheeler magazine published its review of the 1982 Chevrolet Blazer diesel, and sure enough, Detroit’s claims held water, from Four Wheeler:
We wrote that the Blazer wasn’t changed much from the 1981 model, so obviously the engine was the big news. This diesel engine was groundbreaking for GM. The previous 5.7L diesel, found in GM cars and two-wheel-drive trucks, was a reworked gasoline engine, whereas the 6.2L was built from the ground-up for truck use. It was available in four-wheel-drive models, too. The non-turbocharged engine had a power rating of 130 hp at 3,600 rpm and a torque rating of 240 lb-ft at 2,000 rpm.
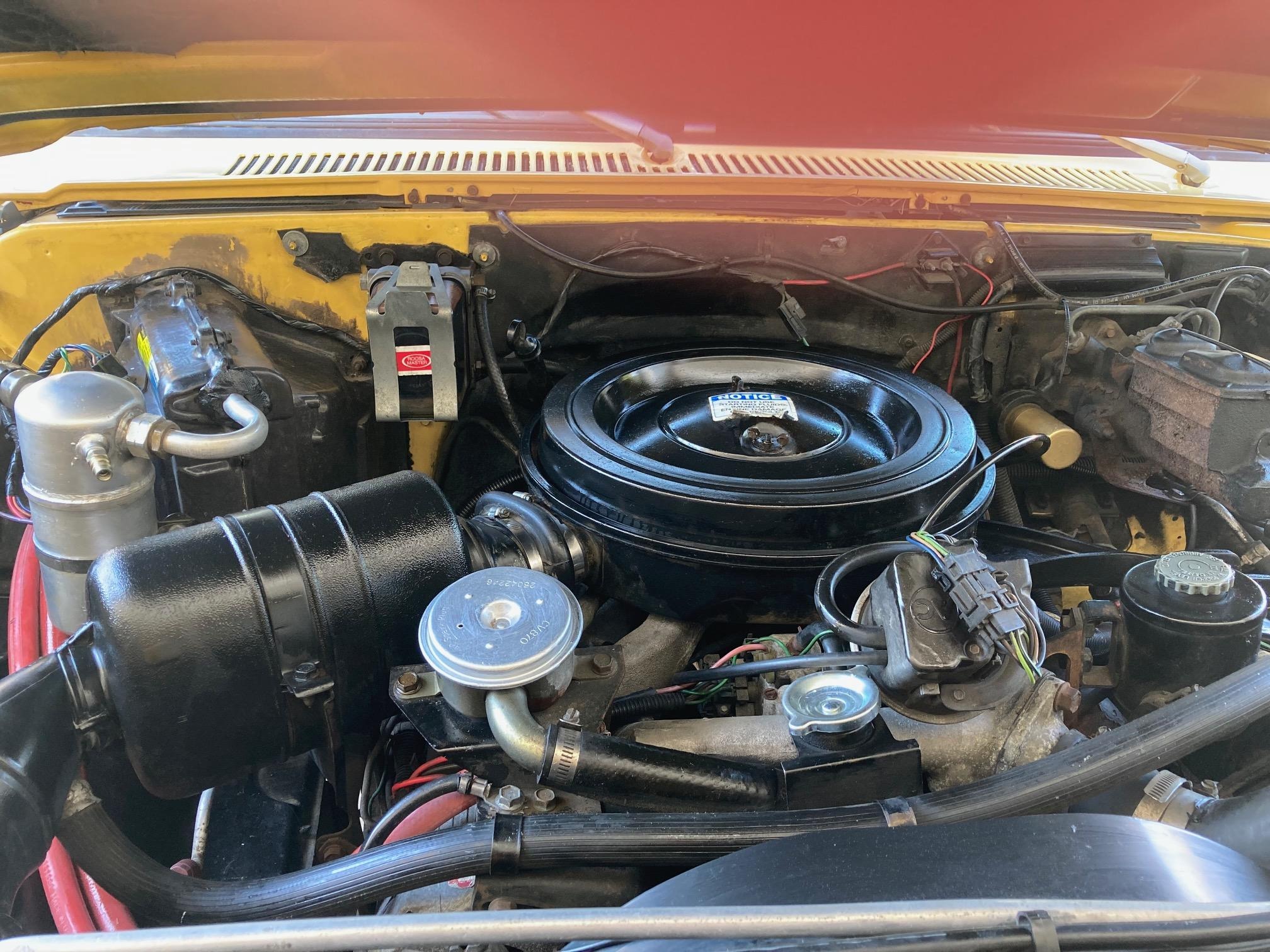
Of these numbers, we wrote, “Both figures are impressive for a diesel, and they are reflected in excellent power and outstanding performance. We can’t stress that enough.” We went on to note that the diesel also returned good fuel mileage. “But the kicker is that at the same time, it delivers fuel economy exceeding the EPA ratings of similar size gasoline engines by about 25 percent.” During our testing, the diesel-powered Blazer returned a maximum of 26.46 mpg on-road and a maximum of 18.72 mpg off-road. The Blazer we tested was equipped with the four-speed overdrive automatic transmission and optional 3.42:1 axle gearing. “With the power this diesel has with a 3.42 axle, we can imagine what it would do with a set of 4.10 or 4.56 gears,” we said.
In some cases, it has been reported that the 6.2 was so thrifty that not only did it achieve better fuel economy than a V8, but it also beat some sixes, too. Depending on the configuration, GM claimed as much as 31 mpg on the highway – but remember, we’re talking testing methodologies that are now more than 40 years old.
Just in case you skipped over some of that, these engines really did have just 130 HP and 240 lb-ft of torque at launch. However, this was before engines like the Cummins 6BT and the Power Stroke 7.3 proved diesels could be powerful and economical.
General Motors was also a pioneer in shoving diesel into a variety of different machines. Detroit 6.2s found homes in half-ton, three-quarter-ton, and one-ton GM pickups and SUVs. Weirdly, Wikipedia claims that there were Impalas with the 6.2, but the only diesel Impalas I could find from the era came from the tail end of the Olds 5.7 diesel. Anyway, at the time, the biggest competition came from International Harvester, which loaded Ford F-250 HD and F-350 pickups with its own 6.9-liter indirect injection V8 diesel. To illustrate how far down GM was on power, a 1983 6.9 IDI made 161 HP and 307 lb-ft of torque. However, those engines were also known for drinking more than their GM competition.
The Detroit 6.2 was also very unlike a modern diesel, and I’m not just talking about its old-school indirect mechanical fuel injection. Starting a Detroit 6.2 doesn’t sound much different than firing up a Cessna 172. The startup procedure involves cycling the glow plugs a few times, waiting for the glow plug light to extinguish, and then turning the key. Remember, the starter has a ton of compression to work against, so, you might have all of 30 seconds to get the engine running before the batteries bow out.
Older diesels like these also don’t like to be run hard. The Detroit 6.2 has a max RPM of just 3,600 when you have a load and 4,000 RPM when the engine is free. But you don’t want to be bumped up on the limit for that long if you want that engine to last.
Unfortunately, GM’s configuration made sense, but not for a long time. In 1987, IH debuted the 7.3-liter IDI V8, which made a healthy 185 HP and 338 lb-ft of torque. In 1989, the Cummins 5.9-liter 12-valve straight-six swung a 160 HP and 400 lb-ft of torque hammer at the competition. Suddenly, GM’s Detroit 6.2-liter wasn’t so hot anymore.
In 1990, the Detroit 6.2 was upgraded to an output of 143 HP and 257 lb-ft of torque in light-duty applications. If you got the engine in a heavy-duty application, you might have been lucky to see 160 HP and 275 lb-ft of torque. Later versions of the Detroit 6.2 saw compression as high as 21.5:1. The Detroit was now an old-school engine, one meant for ranchers to haul stuff for less money. Now, the new diesel competition promised both power and fuel economy, leaving poor GM behind, chugging slowly uphill.
Come 1992, it was time for Detroit Diesel to open its next salvo in the diesel wars. Detroit increased the 6.2’s cylinder bore from 3.98 inches to 4.06 inches. The manufacturer also strengthened the engine’s internals and added piston oil squirters. The new, stronger, and more powerful Detroit 6.5-liter V8 was born.
At its weakest, a naturally aspirated 6.5 made 160 HP and 290 lb-ft of torque. The real fun happened with the factory addition of a turbocharger, which sent HP up to 180 and torque to 380 lb-ft in 1992. Just a year later in 1993, the Detroit 6.2 would finally die while the 6.5 turbo rose to 190 HP and 380 lb-ft of torque.
Improvements in later years came from upgrading the engine to electronic injection pump regulation and trading the Stanadyne DB-2 rotary injection pump for the Stanadyne DS-4, which featured the aforementioned electronic controls. Later improvements included high-flow water pumps and improved thermostats. At its best, a Detroit Diesel 6.5 turbo put out 215 HP and 430 lb-ft of torque.
The power upgrades were welcome, but GM still trailed behind the competition in power. For example, late model 7.3-liter Power Strokes made 275 HP and 525 lb-ft of torque when attached to manual transmissions. Also, like the 6.2, the 6.5s were available in everything from half-ton trucks to military vehicles. The Detroit 6.5 can be found in all sorts of vehicles from the AM General HMMWV to various motorhomes. General Motors stopped production of the 6.5 after 2001, replacing it with the LB7 Duramax, but some motorhomes and commercial vehicles were assembled with the engines into the mid-2000s. AM General is still making a variant of the engine today as the aptly-named Optimizer 6500.
Why People Hate These Engines
So, GM’s 6.2s and 6.5s weren’t really the most powerful powerplants out there, but they did deliver stellar fuel economy compared to an equivalent gas engine. Why will you see no shortage of articles and forum posts hating on these engines?
While Detroit Diesel and GM designed some stout mills, it appears that some of them have not aged well. Diesel Hub notes that the 6.2 can suffer from issues including chronic overheating, cracked engine blocks, and my favorites, failures of the crankshaft, flywheel, or harmonic balancer, the destruction of any of which will turn your 700-pound (dry) 6.2 V8 into scrap in an instant.
Sadly, the 6.5 suffers from a similar list of issues but adds to the fun with possible cracked cylinder heads and failures of the electronic controls. I have personally seen turbocharger failures on a number of 6.5-equipped trucks and RVs. DrivingLine notes other well-known issues from oil pressure switch failures and wastegate failures to engines that either stall out or just fail to start. The publication notes that starting issues could just be failures of your truck’s glow plugs, which is something I’ve also personally seen with a 6.5, but also the truck’s vacuum pump could just seize, wiping out the engine’s serpentine belt with it.
Then there’s just the fact that these trucks are so old now that even if they do have intact electronics, they’re getting pretty crusty, which could cause issues with that electronically controlled injection pump.
So, the Detroits have a sour reputation in the world of diesel pickups. The competition made more power while these engines suffered from sometimes catastrophic issues. As such, you’ll often find one of these trucks for dirt cheap compared to something with a Cummins 5.9 or a Power Stroke 7.3.
That’s not to say that these are bad engines. The Detroit pickup diesels have their fans, especially preppers, who love 6.2s for their total lack of electronics or the 6.5 for its greater power, but still fewer electronics than newer engines. Motor Trend‘s Senior Editor Aaron Gold has a 1983 GMC Suburban with a 6.2 diesel under the hood and while he describes performance as “acceleration is excruciatingly slow” and the engine can’t even hold highway speed on hills, his shows no sign of stopping. Others love tuning these engines because they aren’t just another Cummins or Power Stroke and they don’t require a huge investment of cash upfront.
Enthusiasts have valid reasons to dislike these engines, but don’t discount the power of Detroit Diesel. The modding world for these engines remains healthy, even more than a couple of decades past their expiration date. Banks made a turbo kit for 6.2s as recently as 2018 and you can still buy other turbo kits for these engines today.
The Detroit Diesel 6.2-liter and 6.5-liter V8 engines were never the most powerful or the most popular, but by all accounts, it seems like they achieved their missions. These engines sipped fuel compared to gassers and even gave half-ton truck owners the option to go diesel when the rest of the Big Three locked diesels to bigger trucks. Sure, they weren’t perfect, but they might be worth looking at today if you’re a diesel nut.
(Images: GM, unless otherwise noted.)
“Weirdly, Wikipedia claims that there were Impalas with the 6.2”
The claim is that GM built a few for testing then handed them over to the Government.
Nobody has been able to back this claim up though. If it did happen they likely have been crushed decades ago.
It’s also worth mentioning that GM didn’t originally develop the turbo system for the 6.2/6.5.
Gale Banks was offering an aftermarket kit for the 6.2 that eventually became factory equipment from 1989-1991. They took the design in house for the 6.5.
Has The Ed. Given up on you?
How is that even a title?
At what point in one’s career as an automotive journalist do they throw off all those sterotypical lazy entitled millenial tropes; grow up, and show some professionalism? In this business, one clearly no longer needs to be a professional automotive journalist (aka some manner of engineer) to write effectively. But being a proffesional writer certainly helps.
I ran a 1990 GMC 2500 with 6.2 for over 300k miles with no issues.
Never had to multiple cycle the glowplugs.
No crack block, heads, or crank issues. Replaced harmonic balancer as preventative maintenance –
Killed 2 transmissions, but also used the truck within its design limits.
People can destroy a steel anvil with a rubber hammer – they can also overwork the design limits of a vehicles drivetrain and skip regular maintenance.
Speaking of early diesel truck attempts, my 1953 GMC 3-ton could have been optioned with a diesel – with just three cylinders!
I have owned a ’94 C3500 CC dually 5 speed with the 6.5TD since somewhere around 2009-2010. In those 14 years, it has been running only, MAYBE, 3 years total. Out of nowhere it developed a hard, then no-start. I parked it for years and replaced it, even more stupidly, with a 6.2 Powerstroke.
Eventually, a move necessitated getting the 6.5 running again. I had it towed to a shop after sitting for 8 years or better and they had it running in less than a week for under $500. I was able to drive it for about 6 months until the hard-, then no-, start returned. It’s been sitting in storage now for the last 2 years again. And once again I need to get it running to move it. I’m at the end of my rope with it.
It’s gone from a love-hate to a hate-hate relationship.
You can’t read an article like this without a bowl of Blue Bell ice cream. Nothing like the good ole days.
I think a lot of the people who hate on the 6.2 just wanted it to be something that it wasn’t. It was always a light-duty diesel, not a hauler, and it did its job very well – and my experience of a later 6.2 showed that when it was used as intended, it was very reliable.
In 1993 my father bought one of the last 6.2s in a 2WD Chevy half-ton. It was his primary farm truck for 12 years, before he sold it to me. I drove it for 7 years, often in the Rockies. It suited my needs perfectly, towing a fishing boat and a small cargo trailer, until the transmission failed 7 years later. Not having money to pay someone or time and space to tackle the repairs myself, I handed the truck back over to my newly-retired dad, who replaced the clutch pack himself and got it back on the road.
Dad sold that truck this year. It had more than 460,000 km on the odometer, and the fenders and rocker panels were rusted to hell. The engine? Besides belts and filters, it had gone through two radiators – a weak spot – and a few injectors. Never been opened up. Still started and ran perfectly, and delivered up to 30 mpg on the highway.
Don’t knock the 6.2. Did it deliver the power of Ford’s IH or Dodge’s Cummins? No, but it was meant for a different purpose and if you weren’t towing, it would turn in much better fuel mileage, and do it for a long time. It did the job it was designed to do and with proper maintenance would soldier on for a long time.
If the weak point is replacing the radiator every 150K miles, that’s a very strong weak point.
I think my lifetime average for radiator lifespan is closer to 100K across all vehicles.
… if a radiator replacement at 100k miles is expensive, you might be broke.
When dating my wife (1994), she was driving an ’83 GMC 1500 with the 6.2 diesel/4 speed auto. Two tone tan/beige! Her step-fathers old farm truck. We borrowed it for an extended period a few years later (after my T-Bird got T-boned!). My memory is probably suspect, but I remember getting 30 mpg on the Interstate. By then it had a couple hundred thousand miles on it. NO problems with the engine, but the transmission had been rebuilt twice by then. The only issue I had was having fuel fillers on both sides! Hose wouldn’t reach over, so had to set the nozzle down and do a 180.
Having owned several 6.2 & 6.5 vehicles, I love these engines for 2 reasons:
1) The sound. It’s awesome and unlike anything else out there.
2) It represents an alternate path. A path where engines focused on economy without being miserably underpowered. This engine threaded the needle better than other examples from the era (Diesel Rangers and VWs come to mind, as they were significantly slower than their contemporaries). Compared to a 1982 SBC350 the 1982 6.2 offers about the same power, more peak torque, and significantly more low-end torque. The low-end torque is what you feel when pulling away from a stop sign, and it’s wonderful for offroading. Need to get over a boulder while idling at 585RPM? No problem!
So you have the torque of a 454, the power of a 350, and fuel consumption that beats a 305. What’s not to like? As you said, an arms race developed for powerful towing engines. These engines were never going to keep up, and reliability suffered when GM tried.* Comparing a 1982 6.2 to a 1989 6BT or a 1994+ Powerstroke is disingenuous, but that’s exactly what happened as later engines raised the bar and customers focused on towing rather than cruising.
To me, though, this engine offers a different path. Proof that engines can be much more efficient than folks were used to in the 80s. What if the Big 3 had continued the idea, introducing good commuter diesels for passenger cars? Most buyers at the time were not buying tow rigs. We could have had 50MPG A-body cars, at exactly the time that buyers were flocking to efficient imports. Perhaps Detroit wouldn’t have lost so much market share in the 80s if they would have had more compelling commuter options.
In reality the Olds diesel had already ruined the market for passenger diesels. GM even tried an Olds diesel V6 in the A-bodies. Same horsepower, more torque, looks fine on paper…and it sold horribly. Typical GM, pioneering a great idea and then botching the execution. But in an alternate timeline, if GM was less like GM, the idea just…might…have worked.
*I will note that in stock (low-power) form, the 6.2 is much more reliable than the later attempts to get more power out of this engine family. Failed harmonic balancers can break crankshafts, but this is easily avoided by replacing the balancer before it fails (replacement involves loosening 2 V-belt tensioners and removing 1 bolt). The boosted 6.5 engines had overheating issues (cracked heads and failed PMD units), and a few years have dual-mass flywheel issues. Personally, I’d rather have even a bad-year 6.5 than the spark-plug-eating 5.4 that Ford was offering in that era.