Munro & Associates is an engineering firm known for tearing cars apart to find out how they tick. Of course, now, in addition to the engineering consulting business, the company has a significant online profile, too, so they can use their reach to bring in more expertise to share with us all. In the case of the Tesla Cybertruck, Munro got the opportunity to plop a bunch of automotive heavyweights in front of the camera and simply ask them about how they made the truck what it was.
There’s some serious star power in this video; it’s Munro’s equivalent of that Taylor Swift filmclip with all the A-list celebrities. Unlike that godawful film clip though, there’s actually some interesting content to sink your teeth into. Munro & Associate’s founder Sandy Munro gets the low down from five of Tesla’s executives that worked on design and manufacturing for the Cybertruck — Lars Moravy, VP of Vehicle Engineering; Franz von Holzhausen, head of design for Cybertruck; and Drew Baglino, Tesla’s senior vice president of Powertrain and Energy Engineering. David Mau, VP of Software Engineering, and Peter Bannon, director of low voltage development, also lend their experience to the conversation.


Tesla Had To Somehow Obtain 48 Volt Power Window Motors, Figure Out How To Jumpstart 48V With 12V
Right away, the Cybertruck’s 48-volt architecture is a hot-button topic of conversation. Munro openly noted his disappointment that the Model Y hadn’t gone to 48V, noting his own desire to see the automotive industry make that move in the 1980s. The assembled experts explained that it stayed with a 12-volt architecture due to Tesla’s existing production lines being set up for that. With the Cybertruck being an all-new design, though, Tesla had to establish new manufacturing lines anyway, so going 48-volt made sense. “That’s an opportunity, since we have to go buy new tooling anyway to switch to 48V,” explains Bannon.
Of course, using 48 volts for the low-voltage systems on the Cybertruck required attention to lots of smaller details, too. Parts like motors had to be redesigned to work at the higher voltage for simple accessories like power windows and the windshield wiper. But it also posed challenges that aren’t obvious at first blush. “Even little simple things, like how are you gonna jump the car?” notes Bannon. EVs typically use a low-voltage battery to run the car’s basic systems and connect and disconnect the main traction pack as required. If this supplementary battery goes dead, the car needs to be jumped. But if your low-voltage setup is running at 48-volts how can you get a jump? After all, conventional jumper packs are all built for 12-volt cars. Similarly, that’s all you’ll get if you try to use another vehicle for a jump start, too.
The obvious route would be to design and sell 48-volt jump packs and get them out into the wild, but that would be frustrating for owners stuck somewhere without one. Instead, Tesla simply went the route of designing some fancy power electronics to handle the job instead. “There’s a really nice switch-tank converter circuit that allows us to detect whether you attached a 12-volt thing and boost it to 48, or whether you’ve attached a 48-volt thing and then just jump the car straight away,” says Bannon. Thanks to this additional hardware, it’s easy to jump the car’s low-voltage system even if you’ve only got 12-volt gear on hand.
A Vehicle-Wide Ethernet Setup
The Cybertruck has also introduced a car-wide Ethernet system to handle all its various modules and components on one continuous bus. “We have [a] Gigabit Ethernet loop in the car that connects all of the high-speed controllers in the car,” explains Bannon. “It’s bidirectional for redundancy.” It’s not pure Ethernet, though — like you’d use on your network at home or at work. Instead, it’s managed for more predictable real-time performance to suit the automotive environment. “The way we use Ethernet as a transport is quite fixed and planned… it’s time-sliced. It looks a little bit more like a Token Ring network in that regard.” Bannon also credits the streamlined Ethernet loop design as cutting the mass of communication wiring needed by approximately half.
It has far higher bandwidth than traditional CAN bus systems, and makes all the various messages from the car’s modules available on one interface. “All the data for everything in the car goes over one communication link. You can connect your laptop to it and see everything and it’s all synchronized in time,” says Bannon. It should be a boon compared to some modern cars which feature multiple CAN buses for different modules, such as body control and engine management. The Ethernet loop is even responsible for the entertainment system, too. “Audio flows around on Ethernet, and gets distributed to speakers all around the car,” notes Bannon.
Rust-Free Body Panels: The First Airbender?
The Gigacast front end of the Cybertruck uses threaded inserts that self-tap into tapered holes on the casting itself. No machining is required.
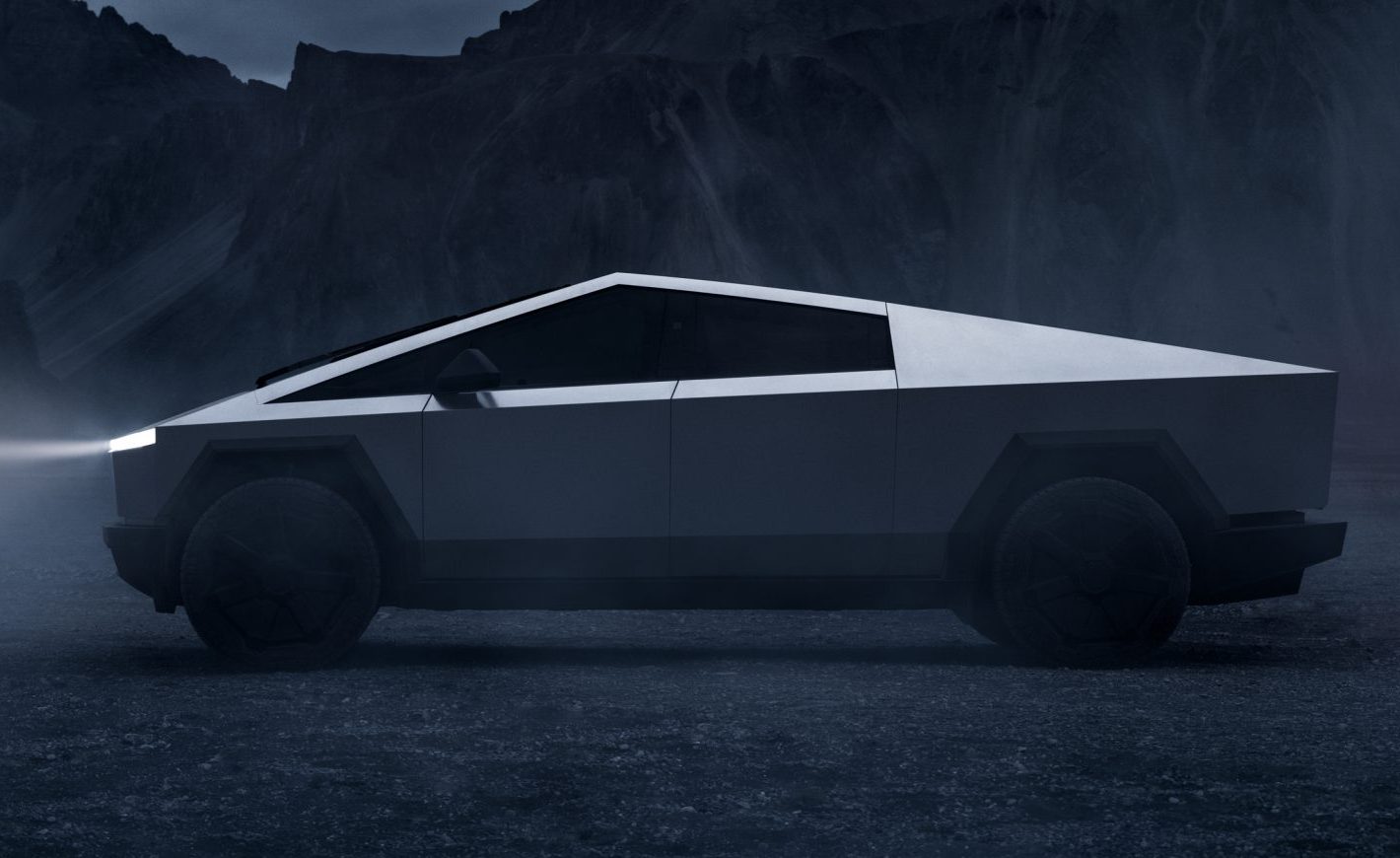
The discussion then moves to the topic of the Cybertruck’s construction. The metal used for the distinctive panels was the subject of much engineering effort early on. “We call it HFS now—Hard Freaking Stainless” explains Lars Moravy. Getting the right combination of manufacturability and durability was a challenge. The material had to be ductile enough to be bendable, but also hold up to abuse, both physical and chemical. “As you know, stainless isn’t stainless… it rusts,” says Moravy. With no paint finish to protect the metal, getting the stainless steel alloy just right was imperative. “We had to make it super corrosion preventative because there’s nothing on it. We balance that, then we add a little more ductility, because when you go full hard, you really can’t bend it that much.”
Forming those panels without marring them on the tooling was a challenge, too. The team came to refer to their process as “airbending,” as Moravy explains. “It looks like a press brake, but we’re shooting high pressure air on a bearing that’s floating the steel, so as the brake moves up and bends it… you get that cushion like an air hockey table almost, so you don’t get the bruises on it.”
Gigacasting: Reducing Press Force Needed, Self-Tapping Threaded Inserts
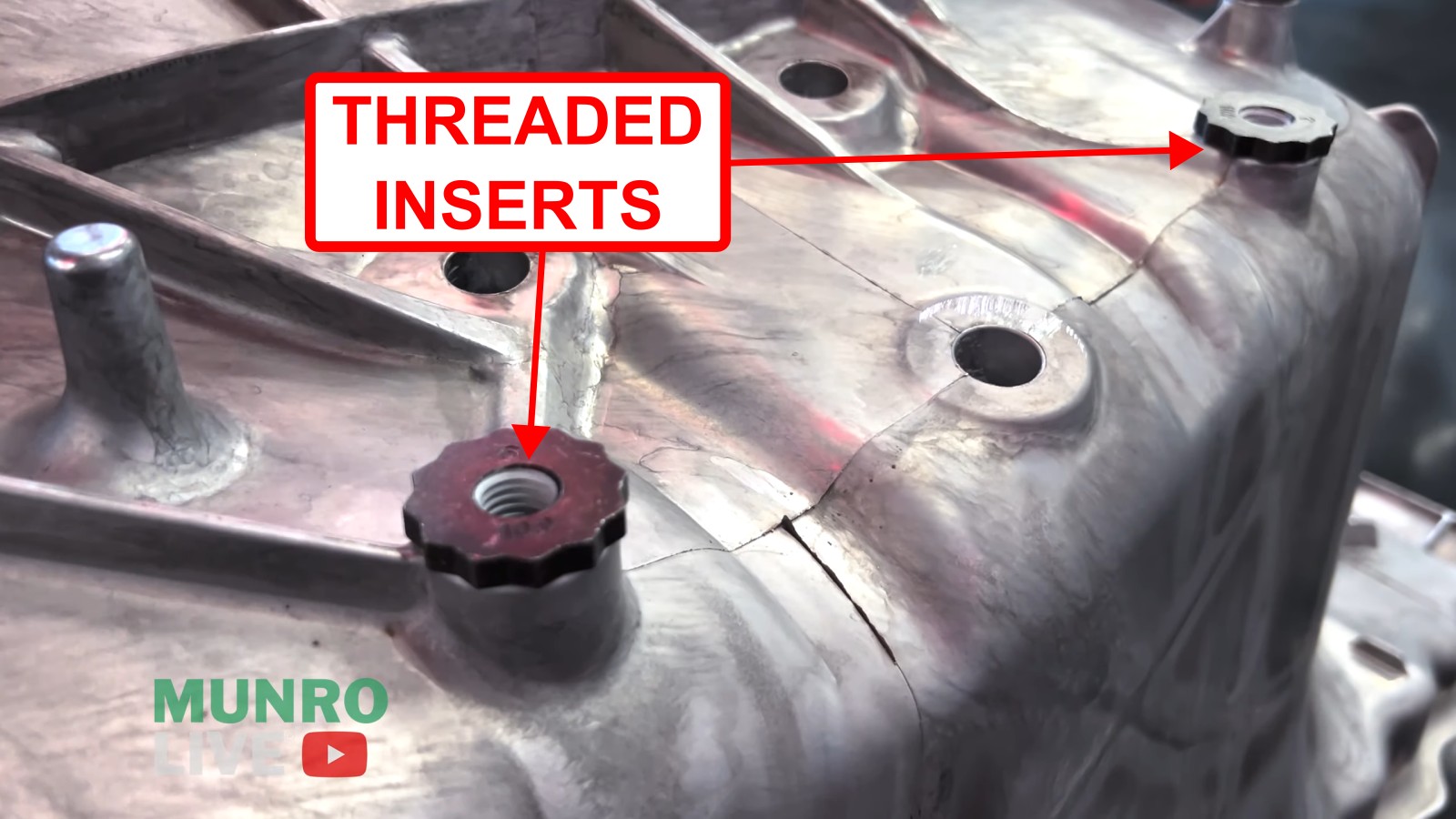
As for the much-ballyhooed Gigacastings, Moravy credits Tesla’s successes in that area to the close pairing between the die designers the engineers who develope the parts themselves. The castings were thus designed from the outset with an eye to the tooling needed to make them, allowing improvements in the manufacturing process. Initially, the team thought they would need to use an 8000-ton casting machine to make the front casting for the Cybertruck, but in the end, casting optimizations got that down to a 6500-ton machine, the same as used on the Model Y. “When you think about tonnage, it’s about how much metal you’re moving… and how fast you’re moving it,” explain Moravy, “But you can restrict that metal flow.” By controlling the way the metal flows through the die, the forces pushing the die apart can be reduced, allowing the use of a lighter-duty casting machine to make the parts. Take a gander at our previous in-depth coverage last month, too.
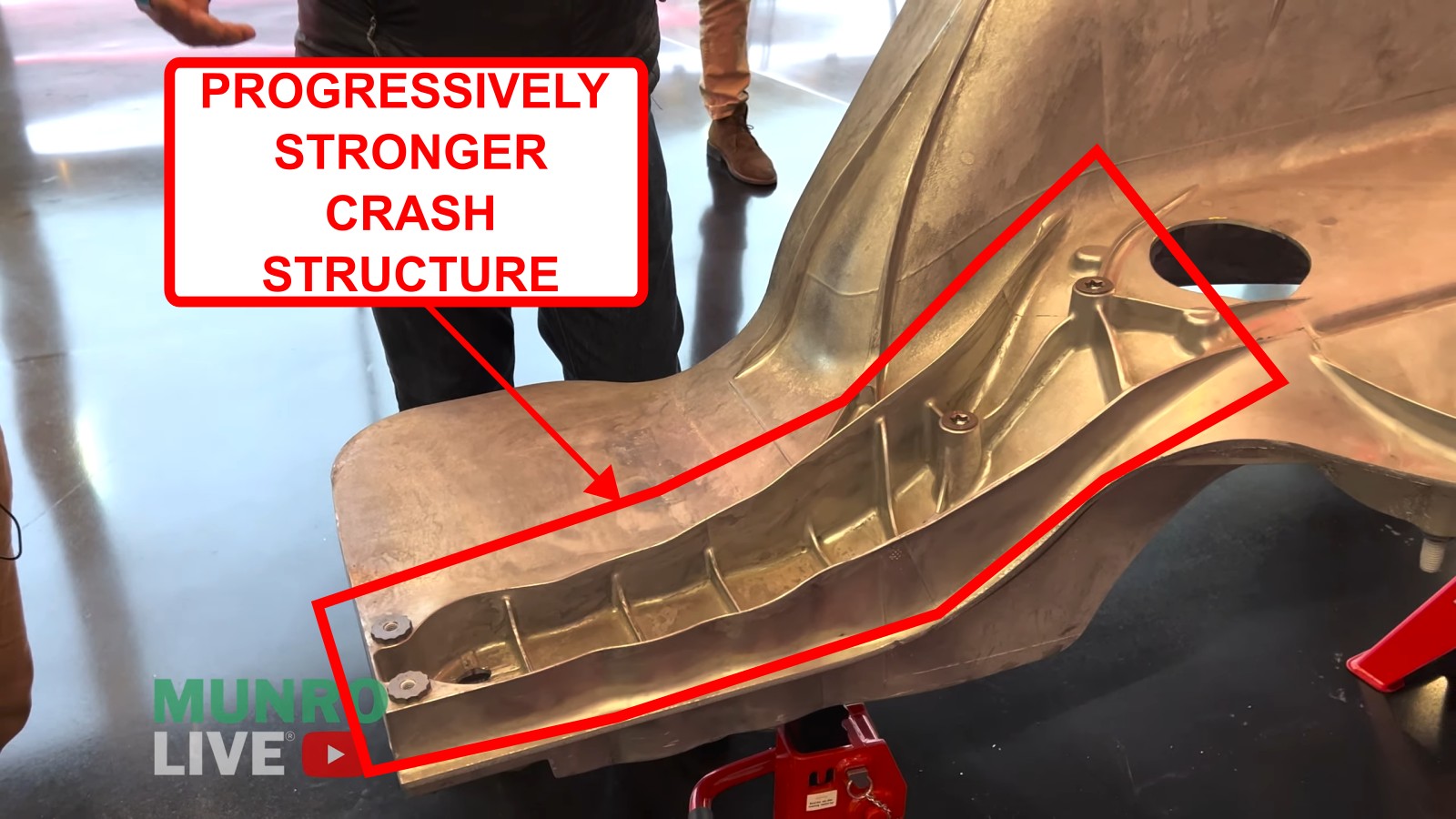
In a neat piece of production optimization, we also learn the threaded holes on the Cybertruck’s front-end casting are achieved with no machining. Instead, the tapered holes are fitted with twist-in threaded inserts that self-tap into the aluminum metal. It’s a neat way of getting accurate threaded holes into a casting with a minimum number of operations. We also get a good look at the crash structure on the rear Gigacast section, where ribs of increasing strength are stacked up in order to absorb energy in turn.
Bigger Vehicle, Smaller Motor Thanks To Shorter Gearing
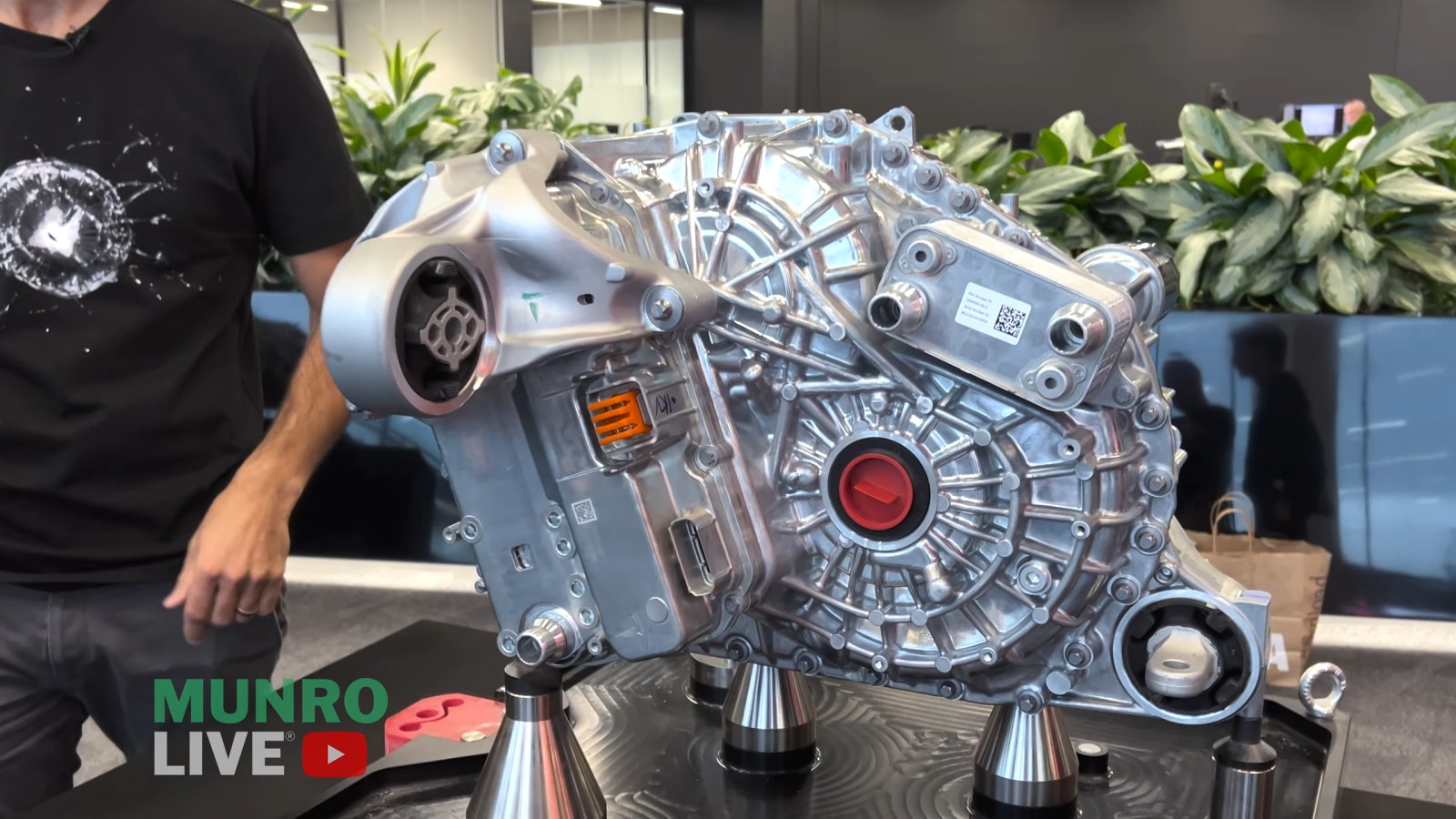
The topic then shifts to the Cybertruck’s powertrain, which should be familiar to anyone across the company’s recent output. It’s highly optimized from a manufacturing standpoint so that all variants share the maximum number of parts. “We have 3 different powertrain configurations, but we only have one PM (permanent magnet) rotor stator, one iron rotor stator, one inverter, and one gearset,” explains Baglino. “With that we can do rear wheel drive, a dual motor, and a tri motor.”
“The actual size of the rotor stator is actually smaller than it is in a Model 3,” says Baglino, explaining that it was tuned to suit the Cybertruck’s required performance parameters. The Cybertruck has a lower top speed than the Model 3, so a smaller motor could be compensated for by changing the gear ratio. Also of note with regards to the Cybertruck is that despite its size, Tesla has made efforts to minimize the amount of expensive materials involved in its manufacture. “We still do have rare earths in the Cybertruck, but the amount of rare earths is no more than that of a Model 3,” says Baglino.
Charging An 800V Truck With A 400V Supercharger, Other Fun Engineering Facts About The Cybertruck
Other neat optimizations in the electrical system include the connectors on the Cybertruck’s controller boards. When disassembled, the main connectors have no plastic housings; instead, the metal pins are stuck on the printed circuit board. The actual mating plastic part of the connector is insteadbuilt in to the controller’s housing, saving material. There’s also a distinct lack of heatsinks, which for much of the low-voltage electronics, is unnecessary. It all comes back to the switch to 48 volts. Raising the voltage cuts the current required to deliver a certain amount of power, and its current that determines heat losses in a circuit. “You increase the voltage by 4x, you reduce the current by 4x, it’s 1/16th the heat.” says David Mau.
We also get a run down of the Cybertruck’s charging and power delivery abilities. It’s able to deliver up to 11.5 kilowatts bidirectionally via the charge port; that’s plenty to run your house if you get stuck without a mains supply. There’s also flexibility in the way the truck adopts 800-volt architecture for its main traction battery. “We actually take the battery and split it in half when we’re at a Tesla Supercharger station that’s a 400 volt station,” says Baglino. “We just directly connect the Supercharger to the battery terminals, whether it’s at 800 volts or 400 volts.” Inside the truck, a hefty dual-pole, dual-throw switch is in charge of configuring the battery into a 400-volt or 800-volt block to allow direct charging in this way.
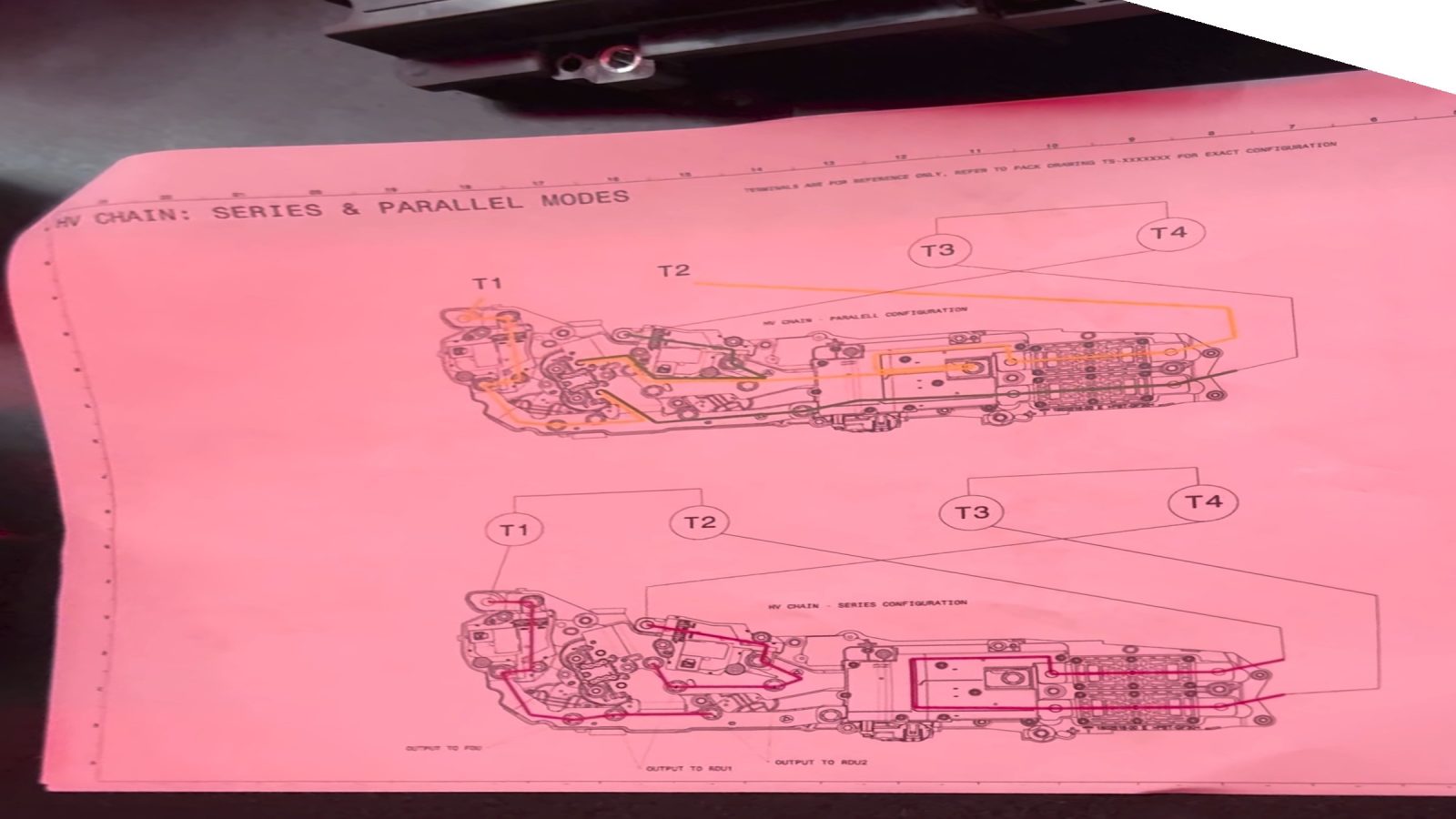
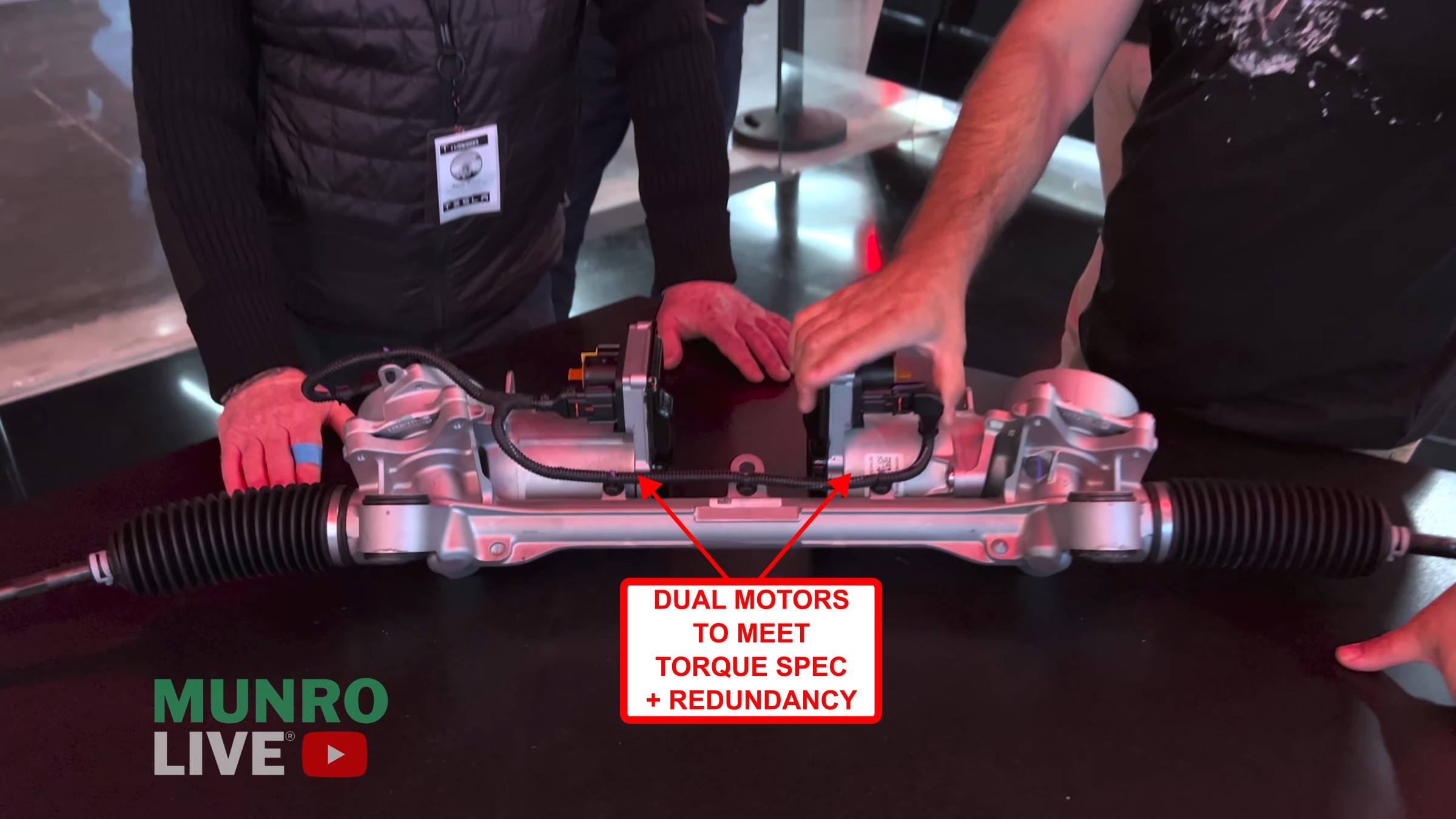
Now that the Cybertruck is finally here, it’s slowly becoming less mysterious. It’s interesting to see a vehicle pulled apart when it varies so much from the traditional construction of those we’ve become familiar with. In time, expect some of the technologies that work to be adopted by the broader industry, while those of middling benefit to be ignored. In any case, it’s always nice to get a guided peek behind the curtain from those who know what’s what.
Image credits: Munro Live, YouTube screenshots
Either this is dumbed down for the interview so much that it doesn’t match what they actually built, or Tesla has done some really hokey, hacky engineering on their communications system. Because if they did literally what it says there, they’re idiots. That kind of custom deviation from a standard when there are perfectly good off-the-shelf solutions available is really bad engineering. What did they gain? Not bandwidth… Not a reduction in wiring (though they claim to have somehow?)… Not some cheap existing solution they could just buy from somebody….
Imagine having to diagnose one of these in a few years when it gets an inevitable rodent infestation.
The Cybertruck’s steer-by-wire system uses two motors, each capable of about 50-60% of the maximum torque required when in parking situations at low speed. If one fails, there is still one motor available to provide redundancy.
Is that a typo? If one motor fails, you only have up to 60% of the torque you would need, so that’s NOT redundancy. Proper redundancy would require each motor to be able to do 100% of the job.
Sounds like it. Guess it would mean you need to apply a little more energy when cranking the wheel. Seems to be designed to mitigate issues at speed, where it matters most, vs parking lot maneuvers. As one of the Camissa videos pointed out, when have you ever heard of a ____-by-wire failure in cars, planes, etc? You haven’t, mainly due to robust engineering and design.
There’s no shaft for you to apply more energy to – you’re arms are just spinning a sensor and if a single motor doesn’t have the torque if the one fails, then the wheels just don’t turn.
Sandy is a sweet old and very wise guy, but I do think he has become a bit of a fan boy lately.
So I’m taking a break from him at the moment, and will return when the Cybertruck craze is over.
He’s got the hots for Elon’s Mother.
I laughed. Nice one! 😀
You think I’m joking.
I’m starting to hate myself for starting to fall in love with the concept of this damned thing. I really just can’t get over the design, so I’m saving my pennies for a Rivian, and hopefully they’ll have all (or most) of the kinks worked out by then-ca 2030.
Couldn’t you just easily jump it using 4 12-volt cars and five sets of cables?
you could certainly do that, but you don’t have to!
That’s way easier than 32 AA batteries!
I’m sure there’s a ton of interesting engineering under the very ugly sheet metal of this truck, but I just can’t get over the fact that it’s so fatally flawed on a conceptual level. EV trucks are a hard sell in the first place (just ask Ford), and this thing isn’t even a truck, it’s more like the student “art” they used to put up around campus when I was in college, which in a rather egregious case consisted of a chair and a sheet of metal welded to an I-beam. A similar amount of effort was put into the design of this thing.
I think to some small extent it actually makes sense given this is much more of a lifestyle vehicle than a true truck. Just look at Rivian Demand vs F150 Lightning demand. Ford has to halve production due to cratering demand because it makes a poor truck value proposition, while the Rivian R1T at similar prices to high spec Lightnings is continuing to sell well, and iirc Rivian reported a majority of R1T buyer were first time truck buyers. Ironically the Maverick is doing the same thing, and yet Ford really can’t seem to figure this out with EVs despite having a truck empire.
The Cybertruck and R1T occupy a similar space in that they aren’t targeting people that need to tow long distance and often, but rather young, affluent and outdoorsy people that want an EV that “can do anything and go anywhere” and in a lot of ways the Cybertruck fits that, but with a Tech Bro spin. Its horrible to look at, and likely will be impractical to own, and awful to repair, but as a car-loving Engineer, the tech debuting on this is really interesting, and it does seem to have a lot of promise and potential to make meaningful change in the industry should it spread.
The only lifestyle that truck is designed for is antisemitism.
I think that’s the bigger issue, yes the truck is weird but weird isn’t always bad. Having an unhinged manic lunatic at the front of the company’s PR will turn off multitudes of buyers, particularly in CA where personal image matters more.
Seems like most people that complain about it on the internet have no intent, or cash flow, to afford one anyway.
I don’t see the point of it, but can appreciate the engineering effort behind it to make it happen.
Will I ever own a Tesla? Probably not due to my tall self not fitting well in both the front and back seats (need to be able to fit myself plus eventually tall teens at the same time).
The biggest engineering issue is whoever designed the damn headrests in the 3 and Y that I sat in a few weeks ago. Why are they not adjustable and why do they stick so far forward so that any reasonably tall person is stabbed in the back of the head with them? I understand the need to keep the headrest close to the head for safety but all bodies are not created equal and nearly every other manufacturer has figured this out and have adjustability built in.
I heard this once, and have no way of verifying it, but I’ve been told the reason that the headrests are pushed forward on cars is so that when you are rear-ended, your neck is bent forward and down, which is preferable to getting whiplash.
Lightning is outselling the Rivian R1T, according to Ford.
They also didn’t halve current production. They halved the production GOAL. They still intend for sales (which had a record month in Nov) to increase from the current 50k/yr rate by 50% to 75k/yr rate.
I’m glad Aang was able to find a job. Good to know Elon Musk is committed to hiring veterans.
Is it possible to go one day without hearing about this dumb thing?
I hate this thing, but you don’t find it fascinating? It’s not just dumb, it’s kind of brilliantly dumb.
You know, that’s it exactly.
Yes. You just need to not read/watch any news or social media.
Hmm — well, it helps if you don’t click on the article’s link.
Wait… so I can plug an EV into my house to power various 110v/220v AC devices, but they can’t figure out a way to run the on-board DC system from the drive batteries?
It seems like they should be able to make a limp-home mode that makes this possible in emergencies.
If I were stranded with 2 tons of batteries waiting for a jump start I would be thoroughly unimpressed – no matter how much the engineers want to high-five each other for allowing you to jump start it with a Civic.
This is how basically all EVs work, as far as I’m aware. There’s a small 12V (48V in this case) battery that can be used to power accessories and is responsible for bringing up enough computers to switch on the big battery. Once that happens everything does run off it, including the charging system for the small battery.
I don’t recall all the details of why, but I assume there’s a safety and vampire drain component. You don’t want a dome light that got left on before winter storage to kill your $XX,000 battery, and you don’t really want energized high voltage lines sitting around while the car is not being used.
As far as I know the Porsche PHEVs use a DC-DC converter to directly power the 12v system and no 12v battery.
EDIT: I’m completely wrong, they have a 12v battery but the traction battery is used to start the car.
It’s primarily supply base also. 12v is the industry standard, so getting commoditized servo parts (wiper and window motors, power seats, radios, lights, etc.) would be very tough on other power systems. Even 48v parts will be something different compared to the rest of the industry, so it’s interesting that Tesla is using a 48v system
No, the onboard electronics do run off the drive batteries. When you charge the drive battery, it charges the low-voltage battery via a DC-DC converter, and that DC-DC converter runs the car’s systems when the car is “on.”
However, for safety reasons, you want to be able to disconnect the traction battery when it’s not in use. That means you need a low voltage system that can run a contactor to connect and disconnect it as needed.
I did a whole piece for Jalopnik back in the day explaining this.
https://jalopnik.com/why-electric-cars-still-use-ordinary-12-volt-batteries-1847209291#:~:text=There's%20No%20Alternator%20In%20Aa%20EV%2C%20There's%20A%20DC%2DDC%20Converter&text=Thus%2C%20having%20a%20source%20of,just%20a%20regular%20car%20battery.
I can understand the reasoning behind it.
I would still be super not happy standing by a rolling battery waiting for someone with a Corolla and jumper cables.
“The Gigacast front end of the Cybertruck uses threaded inserts that self-tap into tapered holes on the casting itself. No machining is required.”
That sound to anybody else like a really fancy way of saying, “This sumbitch is held together with self-tapping screws!”
I know they’re not screws, but still…
Yeah, after reading this, I like this thing even less. I was curious about how they would resolve threading the giant castings, but threaded inserts would have been my cynical joke of an answer. Turns out it’s the real thing. I know they can work, but for major components I simply do not want to trust self tappers in cast aluminum, especially if one adds a corrosive environment, like anything in the snow belt or maybe even warmer climates near the ocean. I’d rather they use adhesive for a lot of it—not like this thing is going to be all that serviceable, anyway. Really, I don’t trust Tesla to do any of this well.
Dissimilar metals threaded together in a salty wet environment with electricity?
It’ll be fine.
Okay while I agree in principle, let’s be clear that these things are far, far from “self tappers”. Threaded inserts like this are used in castings in all sorts of industries and their thread profile is specifically designed to retain maximum strength for the hole depth. The casting will guarantee tear apart around the hole before the insert rips out. Also, the inserts will have a compatible coating with the aluminum (usually a zinc-aluminum alloy of its own so you avoid dissimilar metal corrosion).
Now, whether Tesla used those kinds of inserts or the ones from the hardware store for $0.39 each is up for debate.
The Token Ring network has one bus to run them all.
My Precious.
“Moravy credits Tesla’s successes in that area to the close pairing between the die designers the engineers who develope the parts themselves.”
If they guys designing the parts aren’t designing the tool in their heads while they are doing it, you need to find better design engineers.
Decades ago a guy pointed out to me that the fillets I was scattering all over a casting were dictating the diameter of the ball nosed cutter required to make the tooling. Now I can’t un-see it. You don’t need to compromise towards the tooling all the time, but you should fully understand the implications when you make a choice.
I don’t have any strong feelings about the truck it’s self, but I would have loved to be involved in the project.
I can’t imagine how these giant castings would be designed without the tooling engineers being involved. That must have been a lot of modeling and trial and error to achieve.
I’ve seen castings designed by OEMs with zero involvement by the people who make the tooling. It makes for clunky, expensive, heavy crap. Unless your design team have tooling experience, in which case you get lighter, cheaper, better parts.
There will have been loads of iterations for the Tesla casting, not just for manufacturing feedback, but assembly, integration, NVH and CAE.
I’ve only dealt a little with small stuff, but these things are massive and with such varying dimensions, it’s frankly a hell of an accomplishment. I don’t agree with the idea mainly for repair considerations and long-term durability and corrosion resistance questions, but everyone involved sure deserves to celebrate getting it done.
I don’t have personal experience with it, but I do know people who work in R&D for manufacturing. The stories they tell make me wonder how these companies ever release functional products. A lot of the engineers designing parts have absolutely no idea how the manufacturing process works.
I know a guy who designed a heat shield that could only be screwed on by a tiny technician sealing himself inside it.
So that’s the rattle under my dash when it gets cold!
I’m confused why would an EV ever need to be jumped? In case of a dead battery where an EV can’t drive, I thought they reserved some juice for opening doors and such.
Sometimes your reserve juice runs out.
Sure, but something managing different voltages isn’t rocket science say’s DeWalts Flexvolt.
You can only manage for so long before the power you’ve got left is less than the power required to keep managing it.
Actually, it is. The theory that allowed us to build switching power systems came directly from rocket science — theory of automatic control.
It’s the 12v battery that dies, then it won’t close the contactors for the main pack, so you can’t drive or do DC to DC charging..
Nope, there is an independent battery system from the EV battery to handle all non-drive utilities. There is a DC to DC board that supplies power to the battery as it’s being charged and driven, but eventually that battery will die.
But the move to higher voltage systems is usually for lower amp electronics for various reasons, it may of been a 12v 200a system moved to 48v 50a, having the system convert a 12v jump pack should be manageable and nothing ground breaking.
I’m confused, are you meant to be replying to me? If you’re saying that the car’s battery system should be able to jump off a standalone 12 or 48 volt battery, then you’re correct. It should be able to.
However, this conversion is not a mechanically driven one, it’s electronically driven. The board would need a power source to see voltage from one end and allow the flow of electricity to the other. That board would be controlled by the standalone battery (12 or 48 volt) as a failsafe to ensure that the system isn’t sending electricity at the wrong time causing an overcharge of the battery. So when that 12 or 48 volt battery (whether it be AGM, lead acid, or lithium) dies, then you’ll have to jump it to give enough power to the system to allow the conversion and get the vehicle back up and running.
I own a Volt that has a 360 volt battery pack for the EV drivetrain, along with an ICE that acts as a generator. When the 12v battery starts getting low on voltage, all sorts of crazy CANBUS alarms and issues pop up, including not allowing the vehicle to charge. First thing all Volt owners do is test, and usually replace, the 12 volt battery when these issues arise.
When an EV is in the “off” state, the HV battery contactor opens so that the battery isn’t live. This is good from a safety perspective and to avoid continued discharge. To turn the car “on,” the 12V (or 48V system in the Cybertruck’s case) provides the power needed to close the main HV battery contactor and make the system live again. As other commenters pointed out, once the HV battery is closed circuit again, a DC:DC convertor can be used to charge the 12V battery (the analogous component of an conventional vehicle’s alternator).
EVs have much smaller 12V batteries than conventional cars since the peak power to close the HV battery contactor is much lower than cold starting an engine. The downside is you never experience the feeling or sound of a 12V battery that can barely turn over the engine — a dead 12V in an EV often catches the driver by surprise unless the car warns you before it happens.
Owner of an EV here.
The 12 volt battery on an EV lives a pretty pampered life as it rarely needs to support a high amperage load (the starter). When you start an EV, you’re just powering up the computers and lights.
12v batteries will give you signs of end of life as you notice the starter turning slower on a ICE.
With an EV, they putter along without giving symptoms and then just die (technically, drop below a certain voltage).
The high voltage battery is kept disconnected for safety until the computers decide the systems are good to go. This means there is no way for the high voltage battery to feed the low voltage systems.
So, yes, boosting is still required to get the HV battery online to then feed the low voltage systems during driving.
Munrow&Associates started posting some long anticipated videos this past weekend. I’ve held the firm in high regard, but was utterly disgusted by Sandy’s star struck fawning over Musk, going as far as covering some political views. To be fair, he was in Musk’s factory, and had to show appreciation for the access, but the extent of softball questions, and general adoration was spitakable.
It appears to rely on casting progressively strengthened crush zones. Not being privy to their miracle alloy composition, it would be helpful to see some testing. The elephant issue is how much force does it take for that sail plane dagger to deform? The only crash test video released is front meet wall, and of course the stainless will deform in that scenario. How about multi-car? Expect sky-high insurance rates.
I’m glad I’m not the only one that felt a little cringe watching that video, especially the last 5 minutes of it. I still have tons of respect for Munro’s engineering insights but, well, yep.
Probably unpopular take: I watch a lot of the Munro Live videos on their YouTube channel, and Sandy is by far my least favorite presenter. He obviously knows a ton about manufacturing, but I find him hard to watch in large part because of his deification of Tesla (although based on the comment sections for their videos he might just be playing to his audience…). I also find him frustrating because he’ll rant about something for 20 minutes while not acknowledging the tradeoffs inherent in either his proposed design or the one the manufacturer actually built.
The other people at the company are far more reasoned in their analysis. Every once in a while they can’t explain a bad design decision, but most of the time their talks go something like “This looks weird, but here’s why we think they did it” which is far more interesting to me.
Fair enough.
Munro’s job is to encheapen the shit you buy so that the manufacturer can have more profit. I don’t understand why people fawn over him.
I’ve watched a few of his videos about the Cybertruck, and he seems out of his depth and frankly talks a lot of bollocks regarding non-Tesla OEMs.
I think we’ve found the V-22 Osprey of the automotive world.
The V-22 fleet is closing in on 1,000,000 flight hours. As of last year it had almost exactly the same mishap rate as the rest of Marine Corps aviation, 3.16 per 100,000 hours. The first production aircraft are now 16 years old, and will fly for years to come. The V-22 is, if anything, more capable than the original concepts projected, and it flies missions that would be utterly inconceivable with helicopters. Because of the success of tilt-rotor technology the Army has chosen to use it for the thousands of aircraft that will replace the Blackhawk.
Musk should be so lucky.
As an old USAF Special Operator, I followed the development of the Osprey very closely. As a contractor, I played an early role in developing its aircrew training systems. It is an incredibly capable platform, but also one of the most complex systems ever fielded and is extremely maintenance intensive to keep in the air, which is where I was going with the comparison to Cybertruck: lots of new ideas, new materials and manufacturing procedures that are getting their test run on the Cybertruck, just as the V-22 created new paradigms. It was an expensive and schedule busting path to reach rollout with the Osprey and I think the Cybertruck will have similar teething problems. You mentioned the mishap rate on the Osprey. Firstly, it took years to get where it is today and takes heroic maintenance efforts to keep it there. Secondly, mishap reporting does not take into account all of the long labor and frequent component replacements required to keep the Ospreys flying unless or until there is a loss of life or an airframe. Relying on reported mishaps to accurately assess the overall reliability of the V-22 is misleading. Better indicators are sortie success rate and/or Time in Commission. Here the Osprey is below service average, though not when compared to only rotary wing aircraft, where it’s fairly typical. It’s a complex aircraft that requires special handling to function, but when it does, it’s brilliant. So, no disrespect was intended toward the V-22, just acknowledgement that its advancements come with some heavy costs, and that I believe the Cybertruck fills a similar role in the automotive world, but will not have Osprey levels of support out in that world to keep it rolling. And, yes, Musk – and Cybertruck buyers – should be so lucky.
Very fair and well-said, although that’s a 10-year mishap rate. An AWFUL lot of people without (our) experience have babbled on about the V-22 over the last few days, almost none of them knowing what they’re talking about. So I’m planning on correcting the internet about this issue. I feel pretty good about my chances. 🙂
Absolutely. I group those V-22 detractors with the talking heads who wondered why a car would ever need an 8-speed transmission after that Bentley went airborne a few weeks back.
Repairing this thing after an accident is going to cost a fortune.
Yeah. I was wondering how they plan on frame straightening with current equipment on all those castings. Are they all sacrificial? If not, what is the likelihood that you can rehab a minor wreck without totaling the whole car?
I like the ethernet bus thingy, but so many other engineering decisions seem both unnecessary and too costly. Current industry tech does the job better in many ways.
Castings are like wood or fiberglass/carbon fiber. They are strong, until they are not; once bent to yield, they’re finished as a good component. Sometimes you can weld repair cast aluminum but some little hit that puts a crack anywhere on that huge part is generally going to mean replacing it. I cringe to think of the waste in such an event.
Then as an aside I would like to know how many barrels of oil, total and considering all things, it takes to make that truck vs. an F-150. Hard info to get.
Barrels of oil I don’t know, but the EPA has some very detailed comparisons of total co2 emissions of manufacturing electric cars vs gas cars. The consensus is that it takes at minimum 50,000 miles before the electric cars manufacturing+operating co2 emissions becomes less than that of the gas car. That’s how much co2 emissions are involved in making electric cars. Notice this includes only co2 emissions, not taking into account the big holes in the ground and the extra industrial wastes resulting from manufacturing electric cars.
You can be confident that just the battery in the Cybertruck represents significantly more environmental damage that an entire f150.
I agree, but in the video, at 55:45, one of the Tesla guys shows how to access the cabin air filter from the frunk…. as the cover is removed, the Tesla guy says “we try to focus on service”. That is funny.
Earlier in the video, the electronics guy states that the audio amps for the car stereo are integrated into some master control board. (I have no idea is this is standard, current auto practice).
The efforts in cost reduction have made the vehicle pretty much disposable.
My thoughts on it have always been Tesla doesn’t want to repair these. They will get totaled easily, and then the customer goes back to Tesla and says I want another, and boom Cybertruck sales doubled.
The sales would double if every single one of them was wrecked and totaled, at least. I suspect the rates of vehicle accidents will be statistically similar to most other cars though.
Rate of accidents probably similar to other cars. Percentage of those resulting in the vehicle being written off as totaled probably higher even than other EVs. Collision insurance will be eye-watering.
In the UK, pretty much any crash which leads to a bent frame/chassis, would be an insurance write-off anyway. I don’t see the repairability of the castings being a problem.
On the other hand, the body panels on Tesla’s other vehicles are already very expensive to replace, so I expect repairing body damage to the Cybertruck to be even worse.
(Not that they’ll be selling the Cybertruck in the UK, it’s so big you couldn’t drive it on a car license)
My personal opinion is that the Cybertruck is hideously ugly, purposely difficult to manufacture and repair, portends an era of trucks incapable of doing work, and brings us closer to an electric future that I don’t relish.
All that said, I have immense respect for the engineering required to bring such a flawed vision to life. I legitimately did not believe it would be possible.
Agreed. It’s like they took the lessons they claimed to have learned from the Model X and doubled down on them instead of solving the issues by committing to a body design that’s impractical and polarizing, to put it politely.
“All that said, I have immense respect for the engineering behind bringing such a flawed vision to life.”
Yes, and I look forward to the much more attractive custom bodies that aftermarket converters might figure out how to build around the powertrain/electrical architecture
I agree with you, 100%. I still think it’s a stupid vehicle, but I have to give credit to the engineering and production teams for making this thing possible.
I’m also VERY glad to see that 48v is going to move forward (more) for the auto industry. We had been hanging on to 12v for way too long. That and gigacasting, among other things.
Agreed it’s an engineering marvel, but the end product is flawed. Maybe they are going to use it and their customers as testers for this stuff, so business as normal for them…
Agreed. I don’t enjoy the product, but the engineering is something that others can use and build on (sans licensing etc) and I think that ultimately there can be some really interesting growth from what they have learned. I hope to see it in other products that I appreciate more.
Portends an era of trucks incapable of doing actual work?
I think this can do more actual work than an f150 with a 5.5′ bed. This is car from the first vehicle showing the trend of pickups being less useful. Actually I’d say the pickups that portended trucks incapable of doing actual work were the first generation half ton crew cabs: those 03 or whatever SuperCrew f150s and crew cab cateyes, and the 3rd gen Ram.
A F150’s towing capacity is unaffected by its bed length (apart from weight differences).
It is true that some people buy trucks without doing any actual towing or hauling. Those people disproportionately purchase crew cabs. The truck itself remains capable. Even a Lincoln Blackwood could tow a camper more than 100 miles at a time.
A Cybertruck (which also has a very short bed btw), is actually incapable of towing more than a short distance.
It’s true, electric pickups suck at towing anything longer than medium distances, but that doesn’t mean it’s useless. Not sure where people get this idea that pickups are just for towing.
I do a whole lot of work with my pickup without ever towing a trailer. The bed is there for a reason, after all. Unless hauling tons of rock, building supplies, furniture, tools, ect. doesn’t count as work.
I guess I’m curious what work you believe the Cybertruck will be any better at than a full size gas truck, even a short bed model.
Again, it also has a very short bed.
Payload is OK, but not exceptional. Remember, to get the 2500 lb advertised max, the CT will be above 9000 GVWR, making its competition not F150s, but F250s and 2500 class trucks against which it fares poorly. It will also lose range when hauling heavy, something that is irrelevant with gas or diesel trucks.
We’ll have that answer soon enough. However, there’s one immediate thing to ponder: the price of electricity is much more stable than that of gas, and you can refill it overnight on your own grid. Contractors that don’t have to drive that far (and there are a lot of those) are going to love this thing when the price drops.
That hasn’t helped Lightning sales so far (see article from this morning).
And that truck is marketed much more to contractors than the tech-bros that seem to make up the CT’s customer base.
I like the F-150, but it’s too expensive as an electric vehicle. This is why Ford is doing the T3. They aren’t making money on the Lightning and apparently (my supposition) don’t see a path to profit on that model. I’m hoping the T3 will fix that issue.
The Lightning costs 10s of thousands less than a Cybertruck at the contractor-oriented trim levels. No contractor in their right mind is buying this over a Lightning.
Again, we’ll see. The wildcard is in how well they hold up and how fast the price drops, as well as the charging situation. My ’21 Powerboost hasn’t been great on reliability. We all know who won the charging war, the the CT will benefit from Tesla’s manufacturing methods on cost. My hope is that Fords T3 will learn from all this. I see the contractor uptake hitting in 24 to 36 months as pricing drops and folks get comfortable.
I don’t think a Cybertruck will be better at anything than anything, but I also don’t think it’ll be worse at carrying things in the bed than any other half ton short bed, that is, relatively bad.
A half ton short bed being heavy does not make it compete against 3/4 ton pickups. It’s still a half ton, just an obese one. Not that payload matters, no way you’re getting anywhere near 2500lb in a 6′ bed.
I think it kinda sucks at being a pickup and being useful, but not worse than most other pickups, and I do not think it is indicative of any market shift regarding usefulness.
Regardless of the GVWR, the Cybertruck is priced competitively against the Lightning, and it has a higher payload rating than ANY new F-150, electric or gas.
So, there’s plenty of use cases that the Cybertruck (and Lightning) can fulfill just as well (or better due to superior torque, operating costs, charging convenience, additional enclosed storage, etc.) than similar gas trucks.
That’s not to say it’s the right choice for all buyers or use cases (it’s not), but EV trucks have advantages for many use cases.
You can spec an F150 with over 3000 lb payload, so no, your statement is not correct.
Wrong.
https://www.roadandtrack.com/news/a45103252/why-the-new-ford-f-150-has-a-lower-max-payload-than-the-old-one/
Work often comes with damage. Something built with massive castings is unlikely to be very resilient nor readily repairable (without even getting into Tesla’s limited number of approved repair places and parts availability issues). A truck that can’t shrug off some hits or at least with only some minor repair needed is far less useful, but I doubt anyone who does real work will be buying one of these, especially considering their low numbers will mean parts difficulties real trucks don’t face with their much higher production numbers.
How often do you think people crash their pickups? Repairability issues are a real concern, but I don’t think they’re any more of an issue on a pickup than any other car.
Remember that the competing pickups have aluminum tailgates full of steps, cameras, and motors that cost $4k+ to replace. I don’t even want to know what it would cost to replace an aluminum Ford bed. A Cybertruck would have to be remarkably easily damaged and remarkably expensive to repair to be significantly worse in this regard than the competition.
From a lot of people I’ve known who have done real work, like landscaping, construction, and other kinds of contracting—they think about it a lot because dents and broken lights are somewhat expected. That’s why the contractor grade trucks had sealed beams for so long (maybe still do?). That aluminum bed was a big complaint when it came out and I don’t know of anybody who was interested in the fancy tailgates that cost too much to replace. Of course, that doesn’t matter here as this is a toy for posers, so I might as well be comparing a work truck to a Lamborghini. I’ve probably seen more Miatas and compact cars towing trailers then I’ll see of these doing so and I’ve probably loaded hatchbacks with more than this thing will typically see (admittedly, I’ve loaded the hell out of my hatches and wagons from engines to a yard of dirt in bags).
Dents and broken lights are normal, and I can’t imagine a Cybertruck is so hopelessly fragile that a small dent or broken light could crack a structural casting and total the whole thing. After all, the heavy gauge body panels that are bulletproof and the resulting durability is one of the most marketed design features of the thing.
Again, I think this will be at least as durable as aluminum Fords or light gauge Chevys, and probably won’t be any more expensive to repair than other pickups one the market.
It’s not about fragile, it’s about where one is going to get those replacement parts? Can the repairs be DIY? Tesla’s track record with cars that have much larger production numbers than this will have is terrible in both regards.
People buy trucks to haul things, in the same way they buy SUVs to drive off-road.
This is… fair.
Massive amount of respect for the engineers doing the work, especially in such a flawed environment (Lord knows I’ve been there before, lookin at you Brian.)
But the actual design and execution of everything…
Its gotta be like the lesser cousin of working in the defense industry, manufacturing ammo and such. Working for Boeing or Lockheed, you’ve got moral issues. Working for Tesla you don’t necessarily have moral issues, just… a bitter taste?
I’m sure some of them love the work and have no issues, though.
me: “I love the technology and manufacturing optimization in this thing”
also me: “I hate how much technology and manufacturing optimizations are in this thing”
It’s a design exercise. Is this really that hard to grasp?
Concept cars are design exercises. This is (allegedly, though I haven’t seen one in person) a shipping product being sold to consumers.
It is a real product exercising new design standards into a saleable product. It’s an exercise in a new way to make a Tesla and they are selling it to the world to get some ROI out of it before they trickle the technology down into other models.
We are in an era where most trucks have such short and high bedsides that they are not actually practical for any work but towing. The vast majority of trucks sold are for image and emotional support. I think this truck so exaggerates those qualities with its macho armored car styling and ridiculous “bulletproof” body that it may be peak stupid, and its market failure will lead to future trucks that are actually more practical and functional.
Precisely. People who need a vehicle to accomplish work use commercial van, not emotional support vehicles. This guy, v10, had infamously bad takes in the jalopnik comments section too.
Always nice to be remembered.
Surprised/honored that you can remember my takes yet can’t seem to remember the thousands or millions of commercial pickups that are on our roads every day. Maybe you just have an axe to grind though?
Oh I don’t remember your takes. Just that they were as bad then as they are now.
Lots of pickup trucks gets sold for commercial uses, but that doesn’t mean they are used to WORK. They are used commercially, which this day and age means a manager drives a truck to check up on the people doing all the work from their vans.
This again.
This is just plain false. The majority of pickups are sold for commercial purposes. And a huge percentage of the ones that aren’t are used for work as well.
To clarify, I was referring to the vast majority of private truck sales, not commercial. And while many personal trucks do get some work use, their primary purpose is not being work vehicles. If that was the case they would have longer beds and reasonable ride heights. I’m not saying there are no people using their trucks for work, but I don’t think work use is what is driving the modern pickup market.
What does that have to do with are the trucks capabilities used for work? Commercial purposes =/= truck work.
This isn’t a truck. It’s a Ute.
Trucks have a cab and a frame.