With just hours to go for the current United Auto Workers’ contract, I’ll spend a lot of time today talking about unions, but first I want to address the word that has taken over the car industry: Gigacasting. It’s one of those terms we can thank Tesla for popularizing and yet another example of the company forcing automakers to radically rethink how they do business.
How much of it is Elon Musk’s grandstanding? How real is it? What’s the future of it? Let’s dive in and see.


Tesla Bets Even Bigger On The Future Of Gigacasting
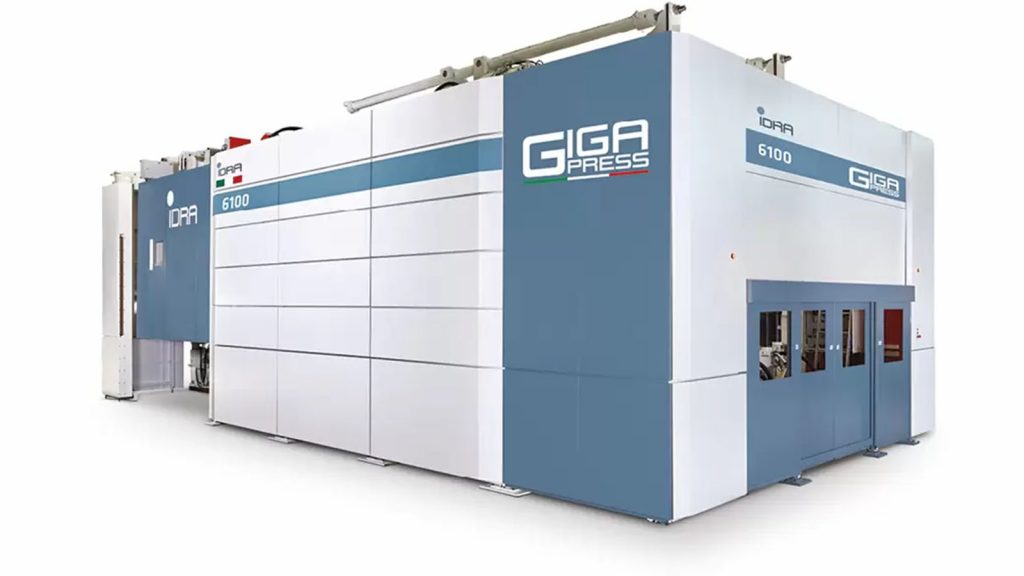
Most of you are likely familiar with the process of casting, which is basically pouring super hot metal into a mold and then cooling it to make a solid metal thing in the shape you want. Humanity has been doing this for thousands of years. It’s also a key part of making cars, though the version of it in use for the last century has mostly been making a lot of small castings and binding them together in some way (bolting, welding, gluing, et cetera).
Gigacasting—which is technically a Tesla term catching on in the wider world—does away with the lots-of-small-castings part by, instead, casting one giant piece. In theory, this has a lot of advantages. If you can make one big cast and skip the labor and energy involved in making a lot of little parts and putting them together you can make cars a lot faster.
This process is key to making electric cars affordable. EVs, as our own David Tracy pointed out to viewers of WJRT-TV yesterday, are not designed like normal vehicles. One key bit with electric cars is that the battery pack in a modern electric car is likely to be a structural element spanning most of what is often referred to the car’s “platform” in a way a gas tank generally is not. It’s an ideal design for gigacasting.
There are big challenges, of course. For one, gigacasting requires giant machines that have to generate 1,000s of tons of pressure to force liquid metal (usually molten aluminum) into a mold that, itself, has to withstand that pressure.
Additionally, modern cars use a lot of hollow structures, both to reduce weight (important for EVs) and to dissipate the energy of a crash. Gigacasting to make hollow shapes is super difficult.
Telsa, in its constant rethinking of the automotive production process, bet big on gigacasting as its method of lowering the cost of creating electric vehicles and, thus far, has been successful in reducing the number of individual parts by hundreds and thousands between models. (Editor’s Note: You think the sparse cabins of the Model 3 and Model Y are because Musk is really into minimalism? Maybe on his spreadsheets, he is. —PG)
So, as the company often does, it’s doubling down. Rather than making a few big pieces out of gigacast molds, they’re hoping to make the entire main structure in one big stamp, like a giant industrial JELL-O mold.
I highly recommend reading this Reuters piece, which gets a lot of sources to talk on the record about the future of Tesla’s gigacasting:
The sources said Tesla’s upcoming small car has given it a perfect opportunity to cast an EV platform in one piece, mainly because its underbody is simpler,
[…]
The sources said, however, that Tesla still had to make a call on what kind of gigapress to use if it decides to cast the underbody in one piece – and that choice would also dictate how complex the car frame would be.
To punch out such large body parts fast, the people said Tesla would need new bigger gigapresses with massive clamping power of 16,000 tons or more, which would come with a hefty price tag and might need larger factory buildings.
The challenges are myriad and, as the article points out, if you screw up the mold it can cost hundreds of thousands of dollars to fix and more than a million dollars to replace altogether.
If it works, though, the savings could be enormous and could help Tesla halve the price of its cars, as Elon Musk has said the company wants to do. This has forced other automakers to try and build cars the same way. Chinese EV brand ZEEKR is doing it. Cadillac is basically doing it with the Celestiq. Toyota is making a huge bet on the technology too, as it tries to keep up with Tesla and the Chinese.
Sure, it’s another example of Tesla hyping a technology that existed before it came around, but in vision and execution, it’s difficult to imagine any other automaker attempting such a big bet without the push.
Also, adding Giga- to everything is silly, but also seems to work. So, in case anyone is curious, we’ve now invented GIGABLOGGING. Please enjoy the GIGABLOGS.
[Editor’s Note: It’s important to reiterate that vehicle body castings are not at all a Tesla invention. I could give you dozens of examples of cast aluminum sections in vehicle bodies, but the one I have on hand is the 2019 Porsche Cayenne (I wrote a deep-dive on it a few years back), which has cast aluminum sections at the front strut towers (a typical location for cast aluminum) and in the rear near the wheel housings. Have a look:
In fact, Tesla started out a bit flat-footed when it came to vehicle body design, with legendary vehicle manufacturing engineers Sandy Munro and Cory Steuben — both from Munro and Associates — noting major problems with the early Model 3 design. Here I am at their facility with my colleague Jason witnessing the unnecessarily complex body comprised of far too many components, which make assembly difficult and costly, and also lead to tolerance stackup problems that could contribute to body panel fitment issues:
Munro suggested that Tesla consolidate all those body pieces into fewer, utilizing a cast design to do so. Tesla took that idea and, as Sandy and Cory make clear in the Gigacasting-themed clip below, turned it up to 11. Instead of just reducing the number of pieces in the rear section by a few parts, they sought to make almost the whole damn rear floor of the car a single cast piece.
“I said ‘This should be one part. One part. And I was talking basically about half this,” Sandy says about his suggestions after seeing the rather suboptimal early Model 3 body design. “And guess what? And guess what? One part,” he continues, showing an updated design.
“But Elon is one of those guys who’s never really quite satisfied, so the one part and the connecting parts, and the other part — the other casting — he felt should be one part. And guess what? That’s what he did over here. This is the …casting for the Model Y. And you can see this is all one part…so he went from no castings to two castings to one casting in the back, and then we move to the front of the car,” he continues, clearly impressed.
“And here we have the front casting…so incredibly well designed. And then he went one step further, and that’s why you see this gigantic hole where a floor usually sits, because again, these guys at Tesla — they take everything that you say literally and then they go and basically implement it…it’s amazing!”
So while Tesla didn’t invent vehicle body casting, it did implement it on an absurd scale, which is why the world is talking about Gigacasting. When was the last time the world cared about casting? That’s just cool in my eyes.
-DT]
Ford CEO: Is Shawn Fain Being Serious?
The impending UAW strike seems even more impending today, with various reports that the strike will probably be more of the strategic variety (i.e., only shutting down specific plants) than a massive walkout.
Credit to Michael Martinez over at Automotive News who has, thus far, done some of the very best reporting on the strike. The story he wrote that dropped yesterday and was updated this morning is no exception, especially for this little bit here:
Ford CEO Jim Farley said the company had put four “increasingly generous” offers on the table since Aug. 29 and had yet to receive “any genuine counteroffer.”
Farley, speaking later to reporters at the Detroit auto show, noted that Fain was not present when he and Executive Chair Bill Ford met with the union’s bargainers.
“There’s still time left,” Farley said. “Whether there’s room in there or not, we won’t know if we don’t get feedback. We don’t understand why we can’t get feedback to make this deal to forge the future.”
Asked if the UAW was negotiating in bad faith, Farley asked rhetorically: “How can you negotiate if you don’t get a well considered, genuine counteroffer?”
There’s a lot to unpack here. First, I want to go back to a TMD I wrote last month with the headline “Is Detroit Ready For A Union Fight With Everyone’s No-Nonsense Uncle?“
But is Detroit ready for this guy and his volunteer JV baseball third base coach schtick? I’m not so sure. I’m wondering if Detroit automakers aren’t going to start missing the older, corrupt generation of UAW leaders.
It seems like the answer is “no,” though I’d like to amend my thought a little because while Shawn Fain is definitely not here to make friends, he’s also at risk of becoming the uncle who seems to be more interested in going on Facebook to rant about his beliefs than actually, you know, doing something about them. A commenter in one of these posts compared what Fain is doing to kayfabe, which is pretty funny.
The question remains how much of this is an act and how much Fain feels, ultimately, that he’s better off striking a bit in order to unify his union.
The Teamsters Won’t Cross Strike Lines To Move Cars For The Big Three
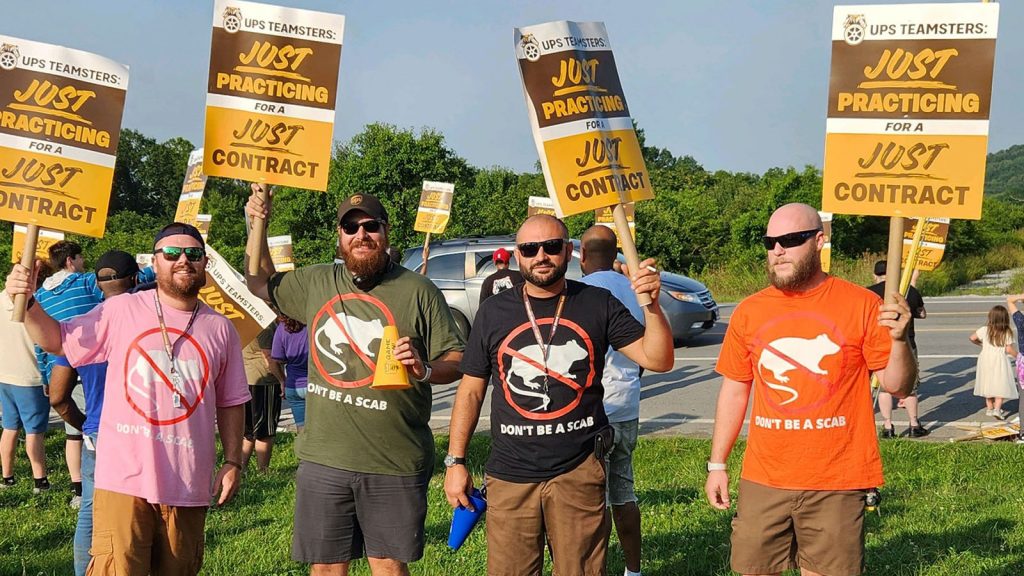
The Teamsters Union has its reputation for a reason, and as someone who is part of a union that is currently on strike (the Writer’s Guild of America, East), I’ve been impressed with just how good they are at striking. I don’t want to get into any details but, yeah, Teamsters know what they’re doing.
The organization is also fiercely loyal to people on strike and, therefore, will not cross a strike line to deliver vehicles for the automakers.
From today’s Detroit Free Press:
“We are 100% supportive of UAW workers and Shawn Fain’s positions,” said Kevin Moore, president of the International Brotherhood of Teamsters Local 299, home of James R. Hoffa in Detroit, which represents 5,000 members and most freight car haulers. “Our Teamsters will not cross strike lines.”
Fain and Moore, a third generation Teamster, spoke at the Labor Day parade in Detroit. Moore’s wife Kathy is a member of UAW Local 245 Research and Engineering in prototype engines. She has worked at Ford 40 years.
Basically, the strike can have a much wider impact than many initially anticipated.
Chinese Government Not Super Pumped About European Tariff Threat
Yesterday we mentioned that the Europeans were looking at ways to use tariffs to make cheap Chinese car imports more expensive. You’re going to be shocked, but this idea was sort of unpopular in Beijing. And by “sort of unpopular” I mean it’s like what happens whenever I wear my Astros hat in Los Angeles. Here’s a fun bit from the Reuters wrap-up:
“China will pay close attention to the EU’s protectionist tendencies and follow-up actions, and firmly safeguard the legitimate rights and interests of Chinese companies,” it added.
Eurasian Group analysts warned that should Brussels ultimately levy duties against subsidized Chinese EVs, Beijing would likely impose countermeasures to hurt European industries.
Other analysts said the probe could slow capacity expansion by China’s battery suppliers, although the move should not pose a big risk for Chinese EV makers because they could turn to other growing markets like Southeast Asia.
“Protectionist tendencies” is hilarious to me as a phrase for some reason.
- The Red Bull F1 Team, Rivian, Me: Who Made The Biggest Boneheaded Car-Mistake?
- General Motors Figured Out How To Make A Great Diesel Car Engine Just To Kill It Too Soon
- The Future Of The Auto Industry Is Electric, With A Gasoline Backup
- I’m Attending My First Ever Formula 1 Race And I Have No Idea What To Expect
Judging by some pictures and reports I’ve seen around online, Tesla figured out a great trick to getting their reject rates back down with the bigger casting: just drop the quality thresholds until the reject rate’s low enough. A few cracks all the way through in high-stress areas? Eh, send it on through anyways.
On the reject rates: Supposedly bad castings can be melted down and re-used on-site without any issues with the materials. I don’t have faith in their QC process in catching all the castings with internal defects or voids, though
For the engineerds out there, here’s a fantastic interview article with a professor from the Technical University of Munich about the advantages and disadvantages of large castings vs traditional methods:
https://www.automotivemanufacturingsolutions.com/casting/forging/megacasting-a-chance-to-rethink-body-manufacturing/42721.article
TL;DR it doesn’t necessarily save cost if you already have equipment and processes dialed in, not all existing factories can accommodate the casting machines, and due to material strengths and design, there isn’t always weight savings
There’s a lot of people asking about repairability, but look where they’re using large castings, it’s mostly the front and rear subframe. They’re the sort of parts that are unlikely to be sold for repairs, and they’re in places where if they’ve got damaged, then the car is probably already a write-off.
Isn’t the way you do a casting where are you need high precision is cast it with a little bit of extra material, then you stick the casting in some sort of a fixture and machine it down to the precise tolerance that you need. The automobile industry has been doing that ever since they started casting internal combustion engines.
Of course, the other thing that you can do is design stuff in such a way that the precision doesn’t actually matter that much. Anybody who is taking apart a 1960s American car will notice that there are an awful lot of washers spacing things together in the bodywork. Void filling adhesive can work wonders in making up for the lack of precision.
Still, repairing these things is going to suck, unless the manufacturer decides to make the frame a wear item. Of course, the manufacturer probably won’t, but you could always pass some legislation to that effect.
Pierce-Arrow was building cars with cast aluminum bodywork way back when Pierce-Arrow was building cars.